July 2007: After what seemed like forever, we finally had the car back together and David decided to go to the chassis dyno to make sure everything on the power side was on track. We fabricated a set of mufflers and added O2 sensor bungs to both collectors to take readings during dyno pulls. The first pull was on the motor only and read 531 hp at the tires. After a few motor pulls we made a pull with the first stage at 300 hp and read 807 hp at the tires. Then we made a pull with adding the second stage at 100 hp and read 900 hp at the rear tire. The air temperature was 87 degrees F and the humidity was 64%. The O2 readings were very safe and there is room for improvement on these numbers just by leaning on the tune-ups a little without being dangerous.
To check out a video of the dyno session, click on the image below:
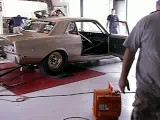
August 2007: We took the Falcon out for a few test runs and on the first pass it went to the left right off the line so the pass was aborted. After a few adjustments, we went back for another pass and went about 300' before the tires broke loose and that pass was aborted. After the seond pass we found out the battery voltage was dangerously low during the run and the battery would not take a charge quick enough to make more runs.
February 2008: Towards the end of 2007 we decided to make some major changes to the Falcon. The changes started with losing weight and evolved into a complete re-work of the front half of the car. We ended up stripping everything off the front of the car but the frame rails and shock towers. We went back with a tubular crossmember with custom Omni rack to cure the bump steer in the original steering. We secured the motor with a front motor plate and mid plate. The mid plate required new headers, and we decided to have them exit the lower front fenders so we could lower the car while keeping them from touching the ground.
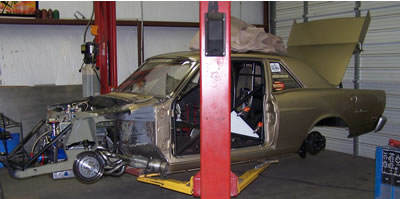
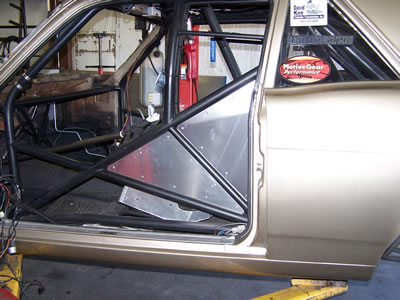
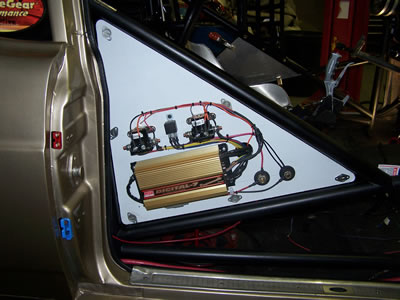
The electrical controls and MSD box were relocated to the passenger side doorway on an aluminum panel between the rear part of the X. The doors were completely stripped to remove any unnecessary material and the stock hinges were lightened and modified to make the doors lift off when needed in the pits. The rear glass was removed and replaced with a piece of MR10 lexan. The bottom of the car was examined and everything that did not need to be there was shaved with a plasma cutter and then ground smooth. There were plenty of small things that we’re leaving out here, but we ended up losing over 200 pounds. What started out as a small project turned into a major production.
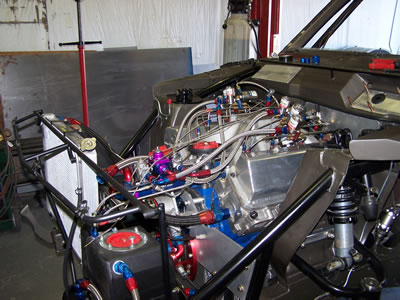
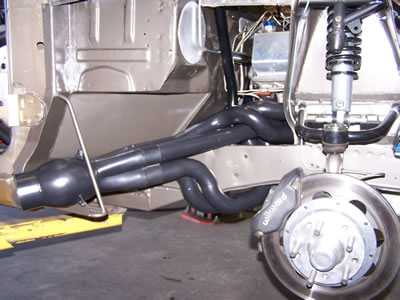
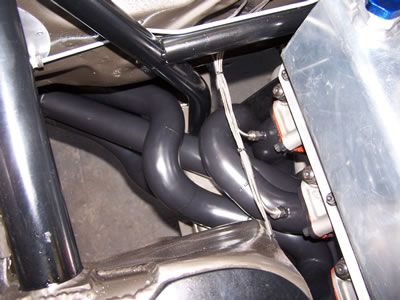
March 2008: We finished everything just in time to run in Pinks All Out San Antonio. The Falcon ran a 5.66 @ 121 mph in the 1/8th mile and 8.98 @ 138 mph lifting early. On the second pass it ran 9.07 @ 148.96 mph. Both runs were with a 100 hp shot of nitrous. The previous best was 5.67 with a 350 hp shot.
photo taken by hotrodshack.com
photo taken by texasdragracing.com
The following are helping with
our project:
SFI 25.5 Chassis Update and Chassis Fabrication
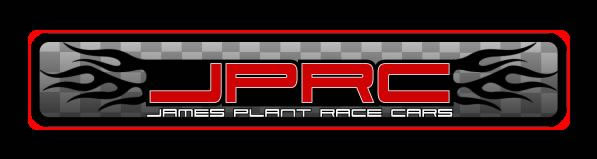
James Plant Race Cars
210-478-8110
Chassis Fabrication
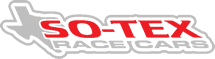
So-Tex Racecars
Mike Clark
210-842-5669
Wheels
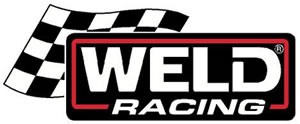
Weld Wheel Industries
6600 Stadium Drive
Kansas City, MO 64129
1-800-669-9353
Nitrous system
and related components